Simcenter FLOEFD
Simcenter FLOEFD Software
Design engineers can expedite the product development process and accelerate a product’s time-to-market by utilizing a complete CAD-embedded CFD software solution for analyzing fluid flow and heat transfer in NX, Solid Edge, CATIA, or CREO without the expensive overhead associated with traditional CFD approach.
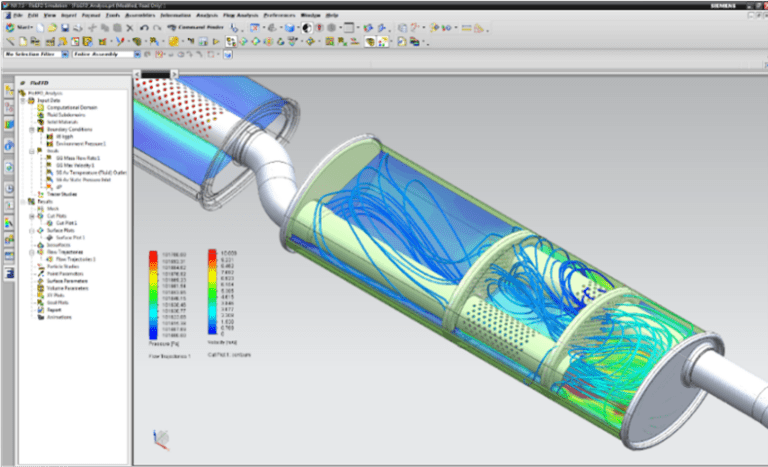
Why Simcenter FLOEFD?
Simcenter FLOEFD is a design-centric CFD simulation tool that offers a plug-and-play solution for CFD analysis by providing a single CAD-embedded environment for design and analysis. By ‘frontloading’ fluid flow and thermal CFD analysis and utilizing native CAD geometry, it can help accelerate the development process by up to 75%. Frontloading involves moving CFD simulation earlier into the design process, which enables engineers to analyze trends and eliminate less efficient design choices.
Empower design engineers with a plug-and-play CFD interface
Enable design engineers to conduct CFD simulations using Simcenter FLOEFD CAD embedded interface, simplified simulation setup, intelligent automation technologies, and easy-to-understand result visualization. Provide them with the ability to investigate design performance at an early stage, empowering them to make informed decisions without the need to overcome conventional obstacles.
Efficiently run CFD simulations directly on native CAD geometry
By allowing designers to modify geometry directly within the CAD environment, Simcenter FLOEFD eliminates costly delays and simplifies the process of preparing CAD geometry for CFD analysis. This implementation eliminates the need for interaction with other geometry tools and reduces the complexity involved in the analysis. As you explore performance enhancements or evaluate changes to the design, the CAD model is updated.
Simcenter FLOEFD leverages SmartCell technology to achieve high accuracy results with a coarse mesh, while its robust automatic meshing system effortlessly captures complex and intricate geometry with minimal user input. This exceptional capability allows it to seamlessly manage small, narrow gaps in assemblies and surface inconsistencies, which typically pose significant challenges in conventional CFD tools. Furthermore, Simcenter FLOEFD’s intelligent automation for pre-processing, including automatic sealing of CAD geometry and leak detection, enhances its efficacy.
Unlock the power of CFD driven design - discover, streamline and perfect
Due to the parametric nature of modern CAD software, a single assembly can be used to drive many different configurations with differing parts or constraints. Simcenter FLOEFD can leverage this parametric configuration capability and tag a CFD project onto each configuration automatically. This makes it easy to analyze different “what if” scenarios and explore more design options within the time available.
With Simcenter FLOEFD, effortless design comparison is achievable through its provision of side-by-side CFD result visualizations, plots, and tabular results, and streamlined report generation. Once the design is optimized using simulation, the CAD model can be efficiently communicated to other engineering functions without delay.
You can think of Simcenter FLOEFD as a productivity solution, “In the time it takes to complete one traditional CFD analysis, you can complete five Simcenter FLOEFD simulations!”
Simcenter FLOEFD Functionality
Automated Meshing
Simcenter FLOEFD incorporates automated methodologies for detecting fluid volumes (no need for negative solid) and generating meshes, specifically designed to seamlessly integrate with CAD geometry. It has the capability to handle intricate or variable quality geometry without requiring model simplification since CAD is used directly for meshing, no need to simplify geometry.
SmartCells Technology is at the heart of Simcenter FLOEFD automated meshing approach by implementing a cartesian immersed boundary grid method. The underlying philosophy is to accommodate multiple control volumes inside a single cell. This is critical for automatically meshing complex CAD geometries, especially when it comes to intersection geometries or very thin volumes.
Automatic mesh refinement is based on different geometric characteristics and adaptive mesh refinement based on the solution is also possible. This can help reduce computation cost (time) without reducing the accuracy of the solution, especially for higher flows and thermal gradients. You may manually specify areas of local mesh refinement if you desire more control over the mesh.
Thermal simulation - LED
LED thermal regulation is crucial to guarantee optimal lighting performance and enhance overall reliability. Specific capabilities and features in the Simcenter FLOEFD LED module include the following:
- Combined thermal-electrical and photometric modeling of LEDs. Accurately calculate hot lumens light output and LED temperature distribution (including LED junction temperature).
- Import measurement data for an RC-ladder compact thermal model from Simcenter Micred T3STER
- Optical characterization data from Simcenter Micred LED Tester to provide the accurate test data-based LED model for use in system level studies
- Calculate Monte Carlo radiation modeling for absorption and scattering of radiation in semi-transparent solids such as glass. Additionally, this functionality accounts for the effects of refraction and specular reflection, while considering wavelength dependency.
- Condensation modeling provides engineers with the capability to accurately simulate the intricate behavior of thin film condensation, evaporation, as well as the impacts of icing and water absorption due to variations in humidity. This is particularly valuable for demanding applications like automotive lighting.
Electronics cooling and thermo-mechanical stress functionality
Simcenter FLOEFD enables thermal engineers and designers to work in the CAD environment to accelerate thermal design – for electronics cooling simulation to thermo-mechanical stress analysis. You can approach the problem from different level of refinement – printed circuit boards (PCBs), detailed (layered), or explicit copper trace simulations- to accelerate simulation speed-up.
SmartPCB offers a distinctive methodology for simulating multiphysics phenomena in a PCB, encompassing electro-thermal co-simulation and thermo-mechanical stress analysis. This approach combines the advantages of a fully detailed (explicit) model, ensuring high accuracy, with significant simulation speed-up. EDA Bridge facilitates seamless import of PCB data from popular EDA software file formats, simplifying the process. Moreover, SmartPCB provides various package modeling options, including 2-Resistor, network assembly, and detailed models, which can be swiftly created, complete with all internal geometric elements, using the convenient Package Creator utility within minutes.
Simcenter FLOEFD offers enhanced functionalities such as transient modeling and measurement calibration, utilizing Simcenter Micred T3STER, to achieve utmost precision. Moreover, the inclusion of BCI-ROM technology empowers users to generate reduced order models from 3D analysis. These models can be seamlessly integrated into electrothermal circuit simulation and system simulation tools, expanding the range of applications, and optimizing efficiency.
Advanced Support
Receive advanced support from engineers that use Simcenter FLOEFD every day.
SDA Software is more than a premier value added reseller of [Product]. We employ award winning engineers that use it every day as part of our professional consulting services. We have the capacity to provide advanced technical support and consulting services to our customers.
Our standard support is included when you purchase a product license or subscription (active maintenance). This covers the following:
- Licensing and setup questions
- Basic technical questions about software features and building models
- Simple troubleshooting.
We understand that for particularly challenging issues more advanced support is required. For this, we also offer advanced support services, which include:
- Detailed help building complex models (even production simulations)
- Extensive troubleshooting, debugging, and testing of models
- Custom consulting projects.
Advanced support is not included with active maintenance.
Meet Ted Blowe, one of our expert engineers
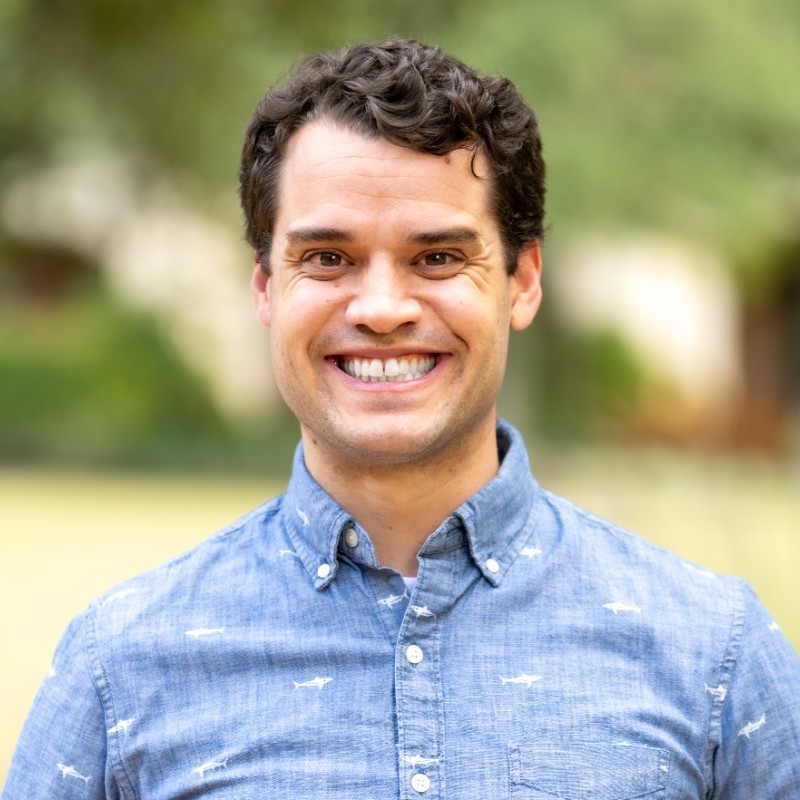
Feature 1
Feature description
Feature 2
Feature description
Feature 3
Feature description